A pre-heater station is one of the most essential tools in any electrical technician’s office. It is an essential instrument for accelerating circuit board repair. Repairing the board would be extremely tough and time-consuming without a pre-heater station.
Each phase is meticulously controlled and refined through technician experience and trial and error, and each phase contributes to solder joint quality and defect reduction. Other industrial soldering tools, however, may not have such precise temperature control. The preheating step is the only thing they have in common.
The preheating stage’s function is to gradually raise the temperature of the entire assembly from room temperature to a soak temperature below the melting point of the solder paste, which is around 150°C.
The temperature is changed at a steady rate of a few degrees per second. The soak phase follows immediately after the preheating phase and keeps this temperature for a period of time to ensure that the board is heated uniformly.
This is followed by the reflow step, which begins the formation of solder joints. Volatile solvents in the solder paste are burned off and the solder flux is activated during the preheat and soaking stages.
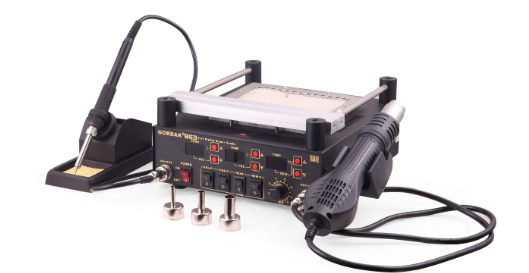
Advantages of preheater stations
1. Allows for the outgassing of volatile liquids
One of the main advantages of preheating is that it allows volatile substances in solder paste to gradually evaporate.
If the temperature change is too abrupt, the rate of outgassing may cause splattering of the solder paste, resulting in the formation of solder balls and a reduction in solder volume on the connections.
Solder pastes containing more solvents may take longer to fully expel these gases, which may justify longer preheat and soak times.
2. Activates the flow of flux
Anyone who has used a soldering iron is familiar with flux, which is what melts off when the iron is applied and is an important component of solder.
Flux cleans the surface of metal contacts by removing oxides, and efficient oxide removal results in clean, strong adhesion and excellent pad wetting. If the preheat temperature is too low, the flux may not be activated effectively, resulting in cold joints and insufficient reflow.
3. Thermal impact is prevented
The primary goal of the preheater station is to raise the temperature of the complete assembly linearly and consistently to the soak temperature.
Continuous heating reduces thermal stresses in both the boards and the components, which is critical for certain packages such as BGAs and other ICs, but SMD chip resistors and capacitors are also prone to thermal shock and may crack as a result.
The existence of thermally sensitive components has the greatest influence.in determining the pace of preheating.
4. Reduces the reflow rate.
Because the complete assembly is at a higher temperature, preheating and soaking can actually reduce the required reflow temperature and duration after soaking.
As localized temperature differences are limited, the temperature gradient when moving to the reflow temperature is reduced.
Compare this to using a soldering iron to attach a through-hole lead to a ground plane. To adjust for heat transfer to the copper plane, the temperature at that point must be much higher, and heating a point to higher temperatures for an extended period of time risks pad lifting, delamination, and burning.
Partner with us for high- quality preheater station
For a standard electrical task, it is critical to use an efficient tool. A pre-heater station is an essential instrument that you should invest in for your job. We create high-quality tools that make labor easier as a reputable manufacturer.
Please contact us if you require a high-quality pre-heater unit. Kindly reach out to us for your quality pre-heater station. Click here to view our products.