In recent times, the need for printed circuit board-based devices has greatly increased. Thus, the complexity of PCB is more than it was before.
Putting in place the required quality and safety check, the manufacturers of PCB are taking extra steps to ensure that they perform optimally.
However, there is a need for rework of the PCB in case of any damage and the ideal tool for this is the use of a preheater rework station because of the preheating system put in place.
They are available in the market but to get a quality one, you need to partner with a reliable and trusted preheater rework station manufacturer.
Many things go into the PCB rework and repair process which are
1. Cleaning
This process is one of the first activities to carry out during a PCB rework or repair. The PCBs may be covered with some dirties which may affect the electrical properties of the device as well as its physical characteristics such as coating, soldering, and bonding.
This can be achieved through the use of the automated method or applying cleaning agents.
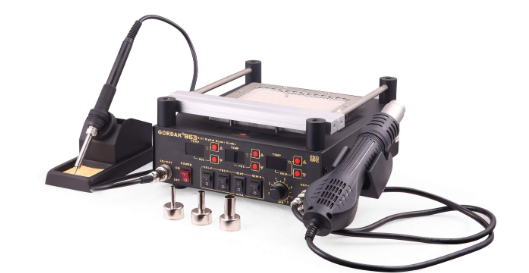
2. Conformal Coating Removal
The removal of the layer is usually the first work carried out during the rework of a PCB device. These layers prevent clouds of dust from settling on the surface from the unfavorable conditions of the environment.
Another benefit of these coatings is the insulation of the device from corrosion. To remove the coatings, various methods can be explored depending on the type of coating used.
These methods are:
I. Solvent Method: This method involves the use of a solvent in removing coatings from a PCB. This is usually effective for coating removal that cannot be removed with a soldering iron.
II. Peeling Method: This process of coat removal is usually apt for thick rubber-like coatings the one made of RTV silicone.
III. Thermal Method: This is the application of low-temperature conditions to remove the dense coating on a PCB. uses a low temperature, a restricted heating method to remove the thick coating from PCBs.
IV. Scraping Method:
This method involves physical means of removing the coatings on the PCB. This is usually achieved using a dental-like.
3. Coating Replacement:
This involves the various means of replacing the soldered coatings on a PCB
4. Baking and Preheating:
The process of baking PCBs before rework is very important as this helps to remove all traces of moisture from the part of the PCB.
As a way of preparing the PCB product for the next activity, SMT components are made to go through a reflow system where the temperature gradually increases and remove the moisture as steam.
I. Baking: In a case where there are chances for the baking process. It should be done before soldering and other activities to help prevent denting of the laminate.
II. Preheating: Preheating improves the sticking of any material to carry out soldering operations efficiently.
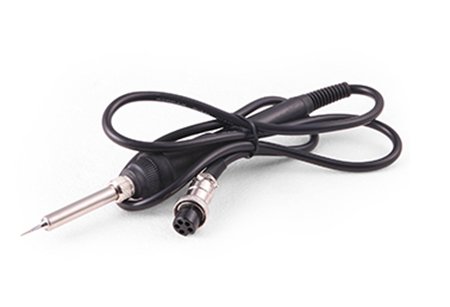
5. Hole Repair
Most times, the plated holes get tampered with during the process of reworking PCB. Hence the need for the proper repair of both the plated hole and none- plated hole aboard. This can be done by either using a transplanted technique or an epoxy method.
While the epoxy technique is used to repair little damages on the plated hole, the transplant method is used to adjust the size, shape, and positioning of the plated hole.
In need of a high-quality soldering rework station?
To carry out the process of repair or rework on a PCB, you need to get the best quality preheater rework station that will not only function effectively but will serve you for a very long time. Hence, the need to partner with a trusted and reliable preheater rework station manufacturer for the best grades.
At Foshan Gordak Electric Co., Ltd. we manufacture high quality and best preheater rework station that is authentic and durable.
Our teams of high-tech experts are recognized globally for producing quality products and nothing short of it. They are fully committed to producing a top-notch rework station. You can count on our delivery of a product which prompt and timely. Kindly click to check our quality products